Efficient Cane Sugar Processing Chemicals: Improve Yield and Quality
Wiki Article
Maximizar Rendimientos Y Minimizar Costos: Estrategias Avanzadas Para La Optimización Química Del Procesamiento De Azúcar De Caña
In the world of cane sugar processing, the search of taking full advantage of returns while concurrently lessening prices stands as a powerful challenge that requires a calculated mix of advanced chemical optimization methods. The details of this endeavor look into the core of performance, where every aspect of the procedure plays an important function in attaining optimum outcomes. By exploring the ins and outs of chemical evaluation, enzyme application, pH control, purification, and distillation techniques, a landscape rich with chances for improvement and technology arises. Among this intricate web of techniques lies the guarantee of unlocking untapped potential and transforming the extremely essence of sugar production. Cane Sugar Processing Chemicals.Chemical Analysis for Efficiency
Chemical analysis plays a crucial duty in improving the efficiency of sugar cane handling by providing crucial understandings right into the structure and homes of the raw materials. By performing in-depth chemical analyses on sugar cane examples, cpus can identify the precise concentrations of sucrose, sugar, fructose, and other parts present in the raw product. This info is vital for maximizing the different stages of the sugar walking cane processing chain, from crushing to condensation.In addition, chemical evaluation enables cpus to identify pollutants such as organic acids, healthy proteins, and minerals that can impact the top quality and yield of the last sugar item. By measuring these impurities, processors can apply targeted methods to get rid of or minimize their results, eventually improving the general performance of the processing plant.
Furthermore, chemical evaluation helps with the surveillance of process specifications such as pH, temperature level, and viscosity, enabling cpus to make real-time changes to make certain optimal problems for sugar removal and crystallization. Generally, a comprehensive understanding of the chemical make-up of sugar walking cane is vital for maximizing yields, lessening costs, and keeping high item high quality in the sugar manufacturing market.
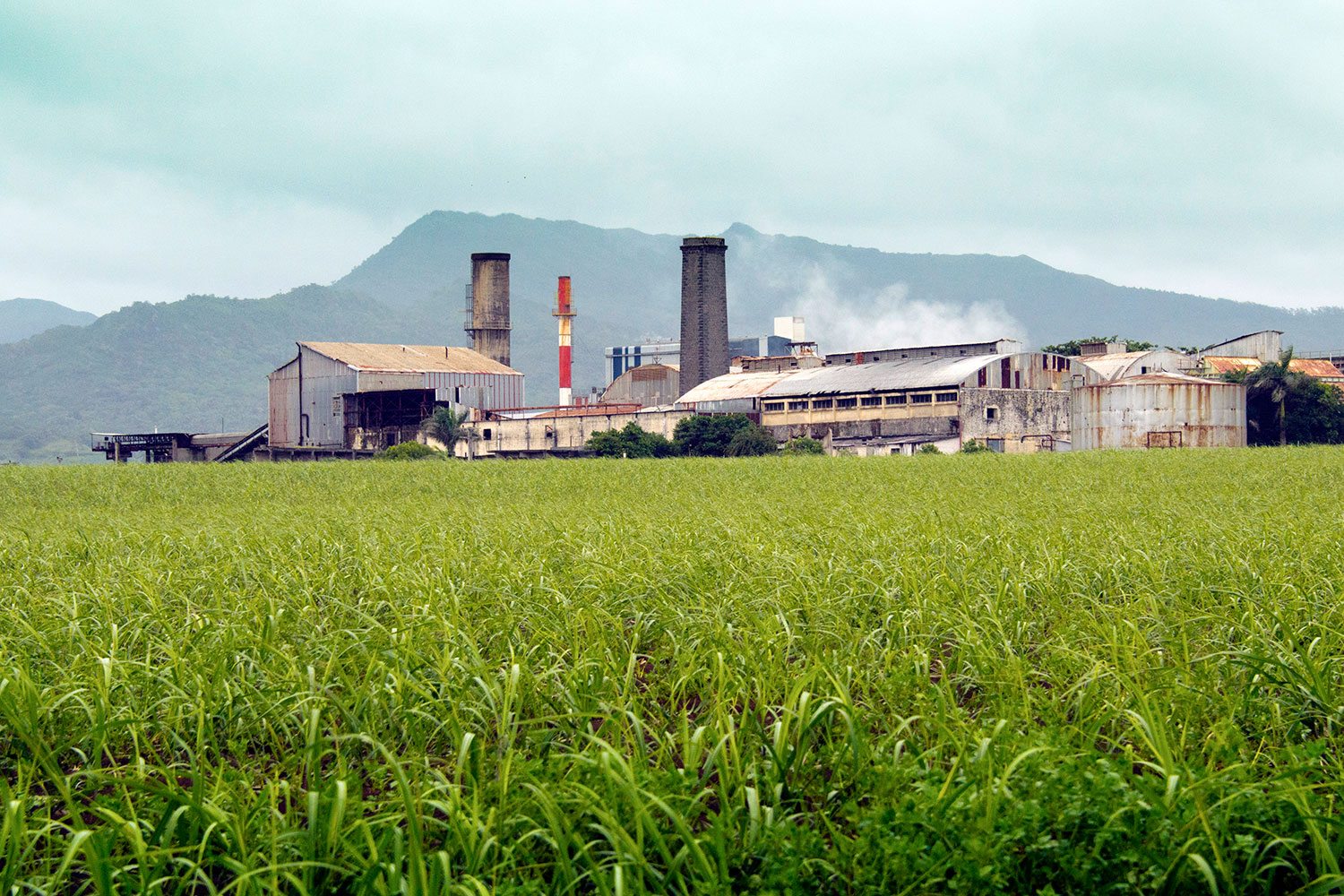
Enzyme Application for Boosted Returns
With a critical method to enzyme application, sugar cane cpus can substantially enhance their yields while preserving operational effectiveness in the manufacturing procedure. Enzymes play an important duty in sugar cane handling by breaking down intricate carbs into easier sugars, therefore boosting the general sugar extraction effectiveness. By including certain enzymes customized to target the different components of sugar walking stick, such as cellulose and hemicellulose, processors can improve the launch of sugars during extraction.Enzyme use provides the benefit of optimizing sugar returns from the raw material while minimizing the power and resources required for handling. This causes a much more sustainable and affordable production process. Additionally, enzymes can aid in decreasing processing time and improving the overall high quality of the sugar item. Via cautious option and application of enzymes, sugar walking stick processors can enhance their procedures to accomplish higher yields and profitability.
Ph Control for Optimal Processing
Enzyme application for raised returns in sugar cane handling lays the foundation for dealing with the important facet of pH control for optimal handling performance. Keeping the ideal pH degree throughout numerous stages of sugar cane handling is essential for taking full advantage of returns and minimizing costs. pH control is specifically critical imp source throughout the removal and clarification processes. In the removal stage, maintaining the right pH aids in attaining effective sucrose removal from the walking stick. Managing the pH throughout clarification aids in the rainfall of contaminations and non-sucrose parts, leading to a purer end product. In addition, pH influences the activity of enzymes entailed in the breakdown of macromolecules, influencing the general efficiency of the procedure. By meticulously keeping track of and adjusting the pH degrees at various handling steps, sugar cane cpus can improve sugar recovery prices, reduce chemical use, and maximize the total manufacturing procedure. Efficient pH control not just boosts the top quality of the last item however also adds to sustainable and affordable sugar walking cane processing procedures.Advanced Filtration Methods
Applying advanced filtration methods in sugar cane handling improves the effectiveness and purity of the end product with improved separation techniques. By including innovative filtration technologies, such as membrane filtration and activated carbon filtering, sugar cane processing plants can accomplish higher degrees of sugar recuperation and improved quality control.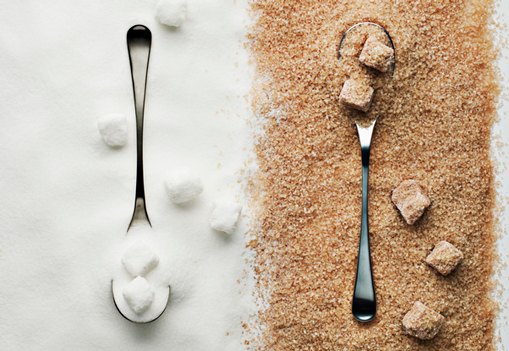
Activated carbon filtering is another sophisticated strategy that aids in the elimination of colorants, off-flavors, and recurring pollutants from sugar cane products. By utilizing turned on carbon's adsorption buildings, this purification approach boosts the clarity and preference of the sugar, meeting the high standards demanded by customers and market laws.
Energy-Efficient Purification Approaches
Energy-efficient distillation methods are crucial for enhancing the sugar walking stick processing sector's power consumption while preserving high-quality item criteria. Typical distillation processes can be energy-intensive, bring about greater production costs and environmental impacts (Cane Sugar Processing Chemicals). Implementing energy-efficient purification techniques, such as vacuum cleaner purification or molecular purification, can considerably reduce energy demands while improving total process effectivenessVacuum cleaner purification involves decreasing the stress within the purification system, which reduces the boiling factor read the article of the liquid combination being refined. This reduction in boiling factor decreases the energy needed for evaporation, causing power savings contrasted to standard purification approaches.
On the other hand, molecular distillation makes use of brief my sources course purification methods under high vacuum conditions to separate substances based upon their molecular weight. This approach is especially effective for heat-sensitive materials, as it runs at lower temperatures, decreasing energy usage and preserving item quality.
Conclusion

Report this wiki page